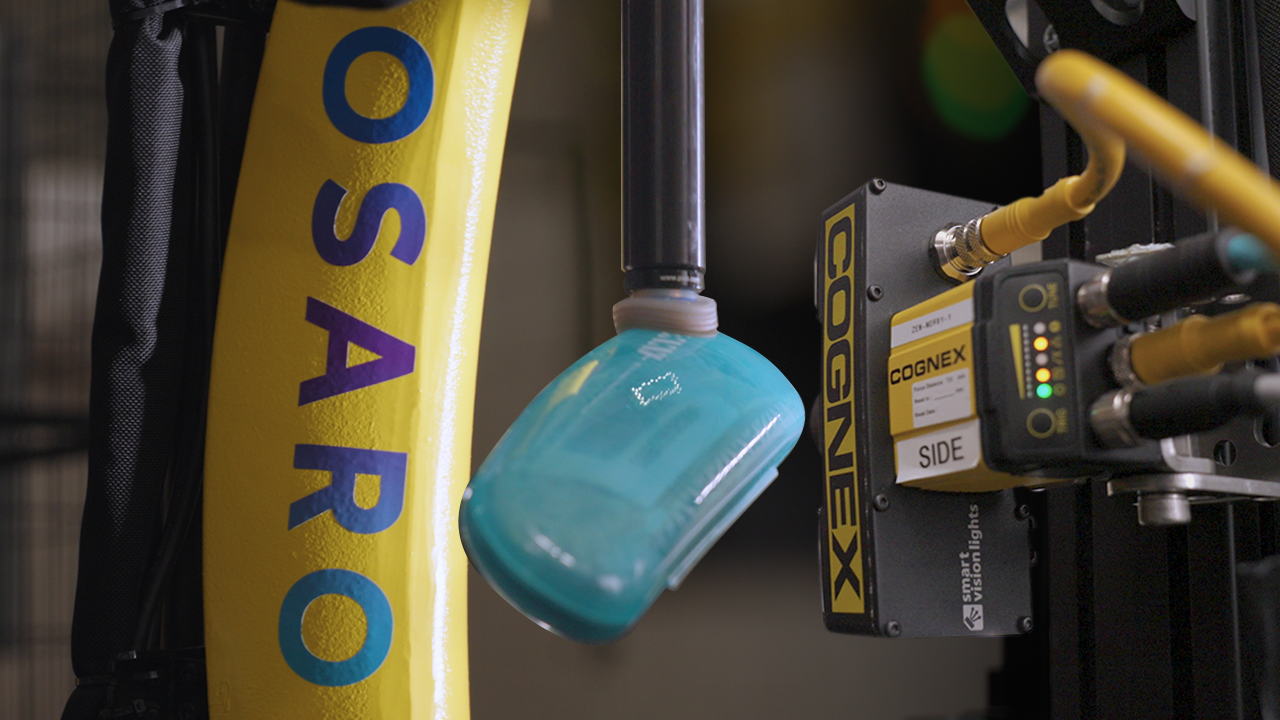
OSARO, a San Francisco-based artificial intelligence and robotics company, delivers robotic picking solutions for e-commerce, specializing in inventories with many SKUs. OSARO’s retail logistics customers face a triple dilemma of labor shortages, high demand, and high consumer expectations. OSARO’s mission is to solve those dilemmas through smarter automation, a low-risk approach, and strong customer care.
One of OSARO’s customers, Zenni Optical, had a unique challenge. Zenni – a leading online eyewear retailer that sells more than 6 million eyeglasses annually worldwide – needed to be able to scan the barcodes on its glasses in cases to process orders. The issue was that the barcodes were located on cellophane-wrapped glasses inside the case and a barcode reader would have to scan through its blue translucent branded case.
Originally, eyeglasses and cases arrived at Zenni and were processed manually with an operator and handheld scanners. The fastest employee could process under 1,800 eyeglasses in a shift, given the need for breaks. Zenni realized they had hit the limits of this manual process and needed a more automated, scalable approach.
Eliminating manual operations with a robotic arm and barcode readers
Zenni sought out OSARO to automate its distribution process with its OSARO® Robotic Bagging System. These fenced-in work cells contain a robot arm, controller, automated bagging machine, and barcode reading technology needed to pick up, scan, and place the eyewear into the bagging machine where it is sealed in a poly bag, labeled, and dropped on a conveyor for shipping. By moving from a manual to robotic process, Zenni achieved 99.9% accuracy by reducing most of the risks inherent in manual processing. Errors were reduced from 20 per 100,000 to less than three per 100,000.
OSARO’s AI-driven robotic arm can easily pick up Zenni’s smooth eyeglass cases. However, since OSARO’s process required reading the barcode through the translucent case, they realized they needed a significantly better barcode scanner to achieve the required rates.
Gemma Ross, VP of operations at OSARO, spearheaded the effort to identify a high-performance barcode reading solution to improve Zenni’s operations. After considering several options to solve Zenni’s challenge, OSARO contacted Cognex because of its ability to maximize read rates.
“Cognex barcode readers are a reliable part of our system. They just work and deliver the highest performance we could ask for.”
OSARO
Increasing Barcode Scanning Accuracy
Cognex knows that every aspect of barcode reading needs to be optimized to maximize read rates. Lighting is often underappreciated as a way of increasing read rates, so Cognex supplies integrated high-intensity LED lights, in this case, a High-Powered Integrated Torch (HPIT). With this lighting capability as part of the barcode reading solution, Cognex readers were able to scan barcodes through Zenni’s glasses cases.
“One of the most important things for my team out in the field is making sure technology is easy to use,” Gemma Ross, OSARO VP of Operations, said. “With Cognex scanners, it’s just so simple to implement, deploy, and maintain. Their support team was always available at a moment's notice.”
Without obscuring the barcode location, the robotic arm grips and picks up the eyeglasses case. It then spins the case in the view of four Cognex DataMan barcode readers, located near the top of the work cell in a C arrangement. The robot arm rotates the case back and forth in view of the readers until one of them successfully reads the barcode.
“I was pretty skeptical at the beginning, but in the end, it came out very reliable,” said Simon Goh, director of distribution and facilities at Zenni Optical. “The whole process was pretty smooth. We don’t really talk about the scanning issue at all in our weekly meetings.”
How Zenni Automated its Order Fulfillment
The robotic system handles 350 to 410 eyeglass cases an hour, with read rates from Cognex barcode readers well over 99.5%. Necessary staffing has dropped from 3 people per cell to 2.
“Honestly, I felt relief when we first started testing with those Cognex scanners,” said Ross. “I was just like, ‘Wow, fantastic, this is one challenge we don’t need to worry about anymore.’ We now have Cognex scanners in all our cells that require barcode scanning. At OSARO, we’re always looking for the best technologies and vendors to incorporate into our strategic partnership ecosystem. Cognex is now part of that partnership strategy, to deploy the best possible solutions to our customers.”
Zenni has now automated its California operation, which handles eyeglass deliveries in the western half of the US. The Ohio operation, handling the east, is next up for an automation transformation.