Menschen, Leidenschaft, Teamarbeit, Integrität und Innovation. Das sind die Kernwerte von American Eagle Outfitters, einem US-amerikanischen Bekleidungseinzelhändler. In den drei Omnichannel-Distributionszentren des Unternehmens in den USA ist Innovation die wichtigste Triebfeder, um Produkte so schnell wie möglich zu den Kunden und in die Geschäfte zu bringen.
Die Einrichtung in Hazleton, PA, ist mit einer Fläche von gut 153.000 m² das neueste und modernste Distributionszentrum des Unternehmens und war das erste Zentrum, in dem die direkte Lieferung an Verbraucher sowie die Belieferung von Händlern kombiniert wurde. Da diese Einrichtung neu gebaut wurde und hohe Erwartungen für den Omnichannel-Betrieb erfüllen musste, waren eine größere Lagerautomatisierung und Effizienz erforderlich, um mit der Nachfrage der Kunden und Händler Schritt halten zu können.
Aufbau eines High-Tech-Vertriebszentrums
Ursprünglich wurde in der Einrichtung eine laserbasierter Barcodelesetechnologie eingesetzt, um Produkte zu scannen, sie an ihr nächstes Ziel innerhalb des Lagers zu leiten und sicherzustellen, dass sie zur Auslieferung in die richtige Warenausgangs-Bahn gebracht wurden. Die laserbasierte Technologie ließ jedoch viel zu wünschen übrig. American Eagle konnte keine Bilder von Barcodes erstellen; daher konnte man die Ursachen für Nicht-Lesen oder Fehl-Lesen oder Probleme mit der Einhaltung der Lieferantenvorgaben nicht lokalisieren. Diese fehlenden Informationen können zu kostspieligen Fehlern oder Nacharbeiten führen, oder dazu, dass Kunden oder Geschäfte ihre Produkte nicht rechtzeitig erhalten.
Der Mangel an Kenntnissen über das Barcode-Lesen veranlasste American Eagle dazu, nach alternativen Lösungen für die Logistikautomatisierung zu suchen. Brian Poveromo, Director of Facilities and Maintenance, machte Cognex als führendes Unternehmen im Bereich der industriellen Bildverarbeitung aus und war von den Möglichkeiten der bildbasierten DataMan-Barcode-Lesetechnologie fasziniert.
„Wenn ich sehe, wo das Problem liegt, kann ich es auch beheben“, sagte er. „Mit einem laserbasierten System weiß man nicht, wo die Probleme liegen, ob der Barcode gut oder nicht gut war, ob es zu viel Reflexion im Bereich des Codes gab usw.“
Poveromo hob die Vorteile der bildbasierten Technologie hervor und verwies auf die Möglichkeit, jeden Barcode deutlich zu sehen und Probleme mit der Einhaltung von Lieferantenvorgaben zu erkennen und zu beseitigen. Der entscheidende Faktor bei der Umstellung der Einrichtung auf bildbasiertes Barcode-Lesen waren jedoch die Leseraten.
Frühere Lösungen, die American Eagle verwendete, generierten Leseraten von 94–95 %, was sich auf die Lieferzeiten auswirkte. Poveromo und sein Team erhielten mit Cognex DataMan Barcode-Lesegeräten Leseraten von 99 %. Angesichts der 96 Millionen Einheiten, die jedes Jahr verarbeitet werden, kann das Unternehmen nun mit höheren Leseraten 3,9 Millionen Fehl- oder Nicht-Lesevorgänge vermeiden. Ab diesem Punkt war die Entscheidung klar.
American Eagle begann mit der Einführung der Cognex-Barcode-Lesegeräte und sah sofort quantifizierbare Vorteile, darunter Effizienz, Zeitersparnis und erhöhter Durchsatz sowie „Soft“-Vorteile wie das Service- und Support-Angebot von Cognex.
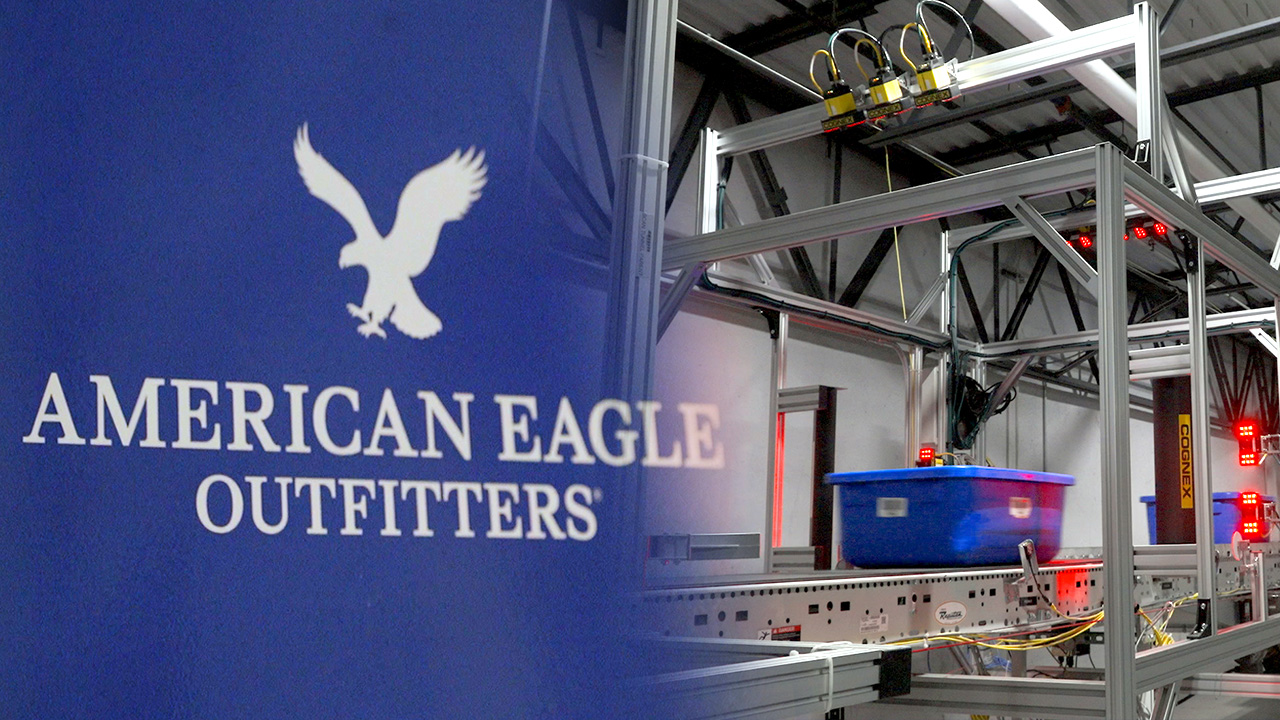
„Die Tatsache, dass wir unsere gesamte Technologie auf Cognex umstellen, spricht für unser Vertrauen.“
American Eagle Outfitters
Unterstützung von Wareneingang, Auftragsabwicklung, Sortierung und Warenausgang mit Cognex Logistiklösungen.
Heute befinden sich in den American Eagle Standorten in Hazleton, PA, Ottawa, Kansas, und in Kanada zu 90 % Produkte von Cognex zur Unterstützung von Wareneingangs-, Abwicklungs-, Sortier- und Warenausgangsprozessen.
Im Wareneingangsbereich verfügt die Einrichtung in Hazleton über 6 Verladetore, die 2 Wareneingangs-Bahnen versorgen. Das bedeutet, dass 6 Lkw gleichzeitig entladen werden können, die sich auf zwei Bahnen verteilen und schließlich auf eine Bahn reduziert werden können. Effizienz und Genauigkeit sind an dieser Stelle entscheidend, damit nachgelagerte Prozesse reibungslos laufen und die Lagerbestände ordnungsgemäß gepflegt werden können. Eine Reihe von DataMan-Barcode-Lesegeräten scannt die Codes und leitet die Produkte in die entsprechenden Bahnen, damit sie eingelagert werden können, bevor sie die Kommissioniermodule erreichen.
„Wenn Karton mit einem Produkt irgendwohin geht, wo er nicht hingehört, verzögert sich wahrscheinlich ein Kundenauftrag.“
Als Nächstes durchlaufen die Produkte den Wareneingangssortierer, in dem Barcodes erneut gescannt werden, bevor sie zu einem der 12 Kommissioniermodule weitergeleitet werden. Poveromo merkte an, dass der Scan, der in dieser Phase stattfindet, für die Geschwindigkeit und Genauigkeit der Sortierung entscheidend ist und Daten an das Lagerverwaltungssystem (WMS) sendet, um zu bestimmen, wohin das Produkt als Nächstes gehen soll.
Nach den Kommissionierstationen gelangen die Produkte zum Vorsortierer, der die Produkte über zwei verschiedene Förderbänder (eines für den Einzelhandel und eines für den Direktvertrieb) durch Cognex-Tunnel zu den Verpackungsbereichen für den Einzelhandel oder den Direktvertrieb schickt. In den Tunneln werden die Artikel auch mit einem Cognex 3D-A1000 klassifiziert und vermessen, um sicherzustellen, dass sie in Bereiche geleitet und gelagert werden, die für ihre Form und Größe geeignet sind. Wenn man z. B. die Abmessungen eines Kartons kennt, ist sichergestellt, dass er in ein Regalbediengerät passt (wobei das Regal 64.000 Kartons mit Kleidungsstücken fasst); wenn man die Maße nicht kennt und den Karton in ein Regalbediengerät zwängt, könnte es zu einem Stau kommen und das gesamte System würde stillstehen.
Auch hier nannte Poveromo Genauigkeit und Leseraten 99 % als die wichtigsten Faktoren für einen reibungslosen Ablauf jeder Phase. „Wenn ein Code nicht richtig oder gar nicht gelesen wird, ist doppelt so viel Zeit für die Identifizierung nötig. Normalerweise gehen wir also zur Bahn mit den Leseausfällen hinüber, ziehen das Produkt heraus und indizieren es erneut.“
Sobald die Artikel verpackt sind, durchlaufen sie einen anderen Sortierer und werden erneut gescannt und zum Versand in die entsprechenden ausgehenden Bahnen weitergeleitet.
Eine kontinuierliche Partnerschaft auf der Grundlage von Innovation.
American Eagle nutzt in seinen drei Vertriebszentren zu über 90 % Logistiklösungen von Cognex und arbeitet daran, jede einzelne Einrichtung auf Cognex umzustellen. Poveromo meinte, dass der Faktor, der American Eagle Outfitters dazu bewegt, Cognex-Produkte immer wieder einzusetzen, neben den Leseraten und der Durchsatzsteigerung der zuverlässige Support und Service war, der ihnen dank der Partnerschaft mit Cognex zuteil wurde.
„Wenn wir bei anderen Partnern Unterstützung vor Ort brauchten, dauerte es 4–6 Wochen, bis jemand kam. Ihnen war nicht klar, dass wir mit jeder Minute, die vergeht, unsere Kunden enttäuschen“, erklärte er. „Bei Cognex können uns darauf verlassen, dass das Problem immer gelöst wird – telefonisch oder persönlich. Die Tatsache, dass wir unsere gesamte Technologie auf Cognex umstellen, spricht für unser Vertrauen.“